3D Printer Tuning: Troubleshooting Made Easy
1. Introduction to 3D Printer Tuning
Why Tuning Matters for Quality Prints
If you’ve ever been frustrated by a failed 3D print and wondered what went wrong, 3D printer tuning is the solution. Think of it as the essential maintenance your printer needs to perform at its best. Without proper tuning, your prints can turn out more like a lopsided pancake than the masterpiece you imagined.
Common Problems Fixed by Proper Tuning
Warping? Stringing? Poor adhesion? These are just a few of the headaches you can eliminate with proper tuning. By fine-tuning your printer, you’re essentially ironing out the quirks that lead to print failures.
Tools You’ll Need for Tuning Success
Before diving in, gather the essentials: a set of Allen keys, a feeler gauge, a calibration cube STL file, and your favorite slicer software. Oh, and patience—it’s your best friend in this journey.
2. Common Problems Fixed by Proper Tuning
Understanding the Root of Print Failures
When your 3D printer isn’t properly tuned, print issues become a common frustration. Proper tuning resolves a variety of problems that can transform your results from frustrating to flawless. Here’s a breakdown of the most common issues and how tuning can fix them.
- Warping
- Warping occurs when the edges of a print lift off the bed, causing distorted or unusable results. Tuning the bed leveling and adjusting print bed temperature settings can effectively tackle this issue. A properly adhered first layer sets the stage for a warp-free print.
- Stringing
- Stringing refers to thin, hair-like strands of filament left between parts of the model. By fine-tuning retraction settings and nozzle temperature, you can eliminate these unsightly strings, leaving your prints smooth and professional.
- Under-Extrusion or Over-Extrusion
- Under-extrusion causes weak, brittle prints, while over-extrusion results in blobs or bulging layers. Both problems can be solved by calibrating your extruder steps (E-steps) and using precise slicer settings.
- Layer Shifts
- If your prints look like they’ve been pushed sideways mid-way through, it’s likely due to improper belt tension or loose axis components. Tuning the belt tension and ensuring proper alignment solves this issue.
- Poor Layer Adhesion
- If your prints are cracking or separating between layers, it’s a sign of incorrect temperature settings or cooling. PID tuning and optimizing fan speeds can greatly improve layer bonding.
Pro Tip: Print a calibration cube to diagnose these issues and track your tuning progress. Each cube reveals specific flaws, helping you zero in on what needs adjustment.
3. Tools You’ll Need for Tuning Success
Essential Tools for Every 3D Printing Enthusiast
Before diving into tuning, having the right tools is like preparing your toolkit before fixing a car—it ensures the job gets done right and efficiently. Here’s a list of must-have tools for tuning success.
- Feeler Gauges or A Sheet of Paper
- For manual bed leveling, a feeler gauge offers precision, but a standard sheet of paper works for quick adjustments. Use these to ensure a consistent nozzle-to-bed distance.
- Calipers
- Accurate measurement is crucial for calibrating filament diameter, checking dimensional accuracy of prints, and adjusting E-steps. Digital calipers are an indispensable tool for this purpose.
- Hex/Allen Keys
- Most 3D printers come with hex or Allen screws. These keys are essential for tightening belts, adjusting extruder components, and fine-tuning moving parts.
- Screwdrivers and Wrenches
- Standard tools like screwdrivers and wrenches are necessary for securing loose bolts and ensuring the printer’s frame remains stable.
- Cleaning Supplies
- A clean printer is a happy printer! Isopropyl alcohol (IPA) is great for cleaning the print bed, while a soft brush or compressed air can remove dust from mechanical parts.
Advanced Tools for Precise Tuning
- Digital Thermometer
- Verify your printer’s temperature accuracy to prevent heat fluctuations that can ruin prints. A digital thermometer can confirm whether the hotend and heated bed reach their target temperatures.
- Belt Tension Gauge
- Proper belt tension is critical for avoiding layer shifts. A tension gauge ensures your belts are neither too loose nor too tight.
- PID Tuning Software or Plugins
- Tools like OctoPrint or Teaching Tech’s Calibration Guide make PID tuning easier and more accurate.
Budget-Friendly Alternatives
If you’re working on a budget, you don’t need to buy everything. Simple tools like a ruler for measuring filament or DIY hacks like using a playing card for leveling can work surprisingly well.
4. Preparing Your Printer for Tuning
Starting with a Clean Slate
Before diving into 3D printer tuning, start by ensuring your printer is in pristine condition. A clean and well-maintained printer is foundational to effective tuning and high-quality prints.
- Clean the Print Bed:
- Use isopropyl alcohol (IPA) to remove dust, grease, and filament residue from the bed. A dirty print bed can lead to poor adhesion, which often results in warped or failed prints. For stubborn residue, a scraper or glass cleaner can help, but be cautious to avoid scratches.
- Inspect and Clean the Nozzle:
- A clogged or partially blocked nozzle affects filament extrusion and print quality. Heat the nozzle to the recommended temperature for your filament, and use a cleaning needle or small wire to remove blockages. Alternatively, consider a cold-pull technique using nylon filament to clear any buildup.
- Lubricate Moving Parts:
- Apply a small amount of lubricant to rods and bearings to ensure smooth motion. Dust and debris can cause wear and tear, leading to inconsistent movement that affects print quality.
Checking Your Printer’s Firmware
Firmware acts as the operating system of your 3D printer. It controls how the printer interprets G-code and manages mechanical movements. Keeping it updated is crucial for optimal 3D printer tuning.
- Why Firmware Updates Are Necessary:
- Firmware updates often introduce new features, fix bugs, and improve compatibility with modern slicing software. For instance, an updated firmware might include advanced tuning features like mesh bed leveling or PID tuning for stable temperatures.
- How to Update Your Firmware:
- Identify Your Current Version: Check the printer’s control screen or refer to the manual to find the firmware version.
- Download the Latest Firmware: Visit the manufacturer’s website or trusted community forums to download the correct firmware for your printer model.
- Flash the Firmware: Transfer the firmware to an SD card or connect your printer to a computer. Follow the manufacturer’s instructions to install it. Always double-check compatibility to avoid bricking your printer.
- Benefits of Custom Firmware:
5. Detailed Firmware Guide
The Importance of Firmware in 3D Printer Tuning
Firmware is the software that controls your 3D printer’s hardware. Think of it as your printer’s brain, dictating how every component behaves. Outdated or improperly configured firmware can lead to issues like poor print quality, slow performance, or even hardware malfunctions. Regular firmware updates unlock new features, improve stability, and enhance the overall tuning process.
How to Check Your Firmware Version
Before updating or customizing your firmware, you need to know your current version:
- Navigate to your printer’s display screen and find the “About” or “Info” section.
- Check for the firmware version number, which is often displayed as something like Marlin 2.0.9 or Creality V4.2.2.
Updating Your Firmware Step by Step
- Identify Your Printer’s Firmware Type:
Popular options include Marlin, Klipper, and custom manufacturer firmware like Creality’s. - Download the Latest Version:
Visit the official website or a trusted community source (e.g., Marlin GitHub page) to get the latest stable release. - Prepare Your Hardware:
You’ll need a USB cable or an SD card to transfer the firmware to your printer. - Flash the Firmware:
- For most printers, load the firmware onto an SD card, insert it into your printer, and reboot.
- Follow any on-screen instructions or prompts during the process.
- Verify the Update:
After installation, check the firmware version on your printer’s screen to ensure the update was successful.
Benefits of Custom Firmware
Custom firmware like Marlin or Klipper can take your printer to the next level:
- Advanced Features: Enable mesh bed leveling, filament run-out detection, and linear advance.
- Improved Precision: Better control over movement and extrusion for flawless prints.
- Greater Flexibility: Customize settings to suit your printer and specific projects.
Understanding Printer Components and Their Roles
Get familiar with your printer’s parts: the hotend, extruder, belts, and stepper motors. Each plays a role in achieving that perfect print.
6. Step-by-Step Guide to Tuning Your 3D Printer
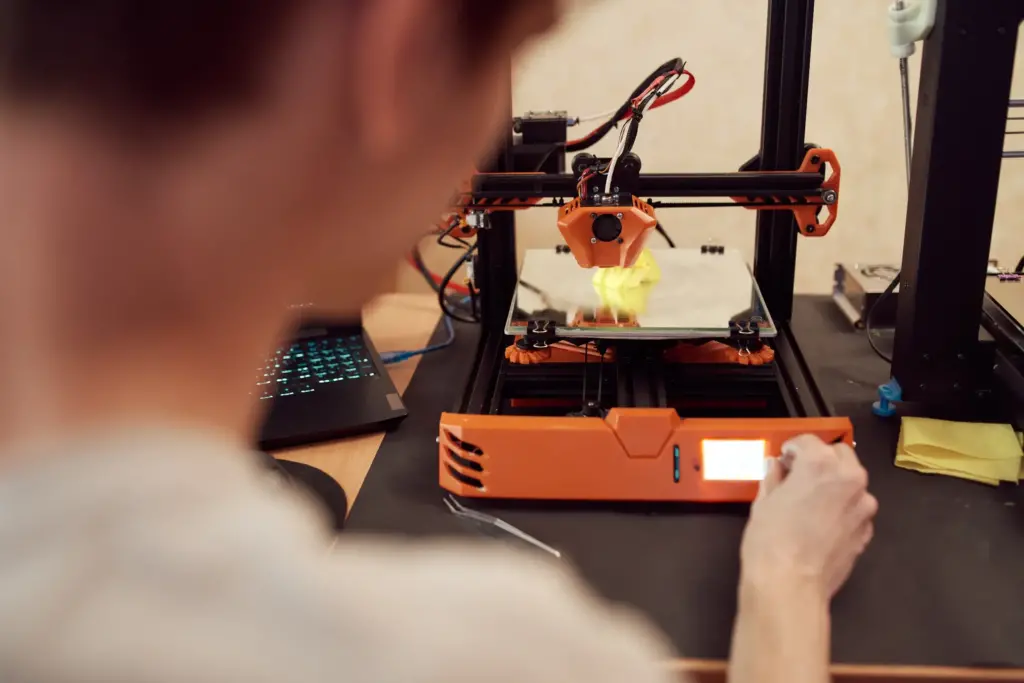
Bed Leveling: The Foundation of a Great Print
A level bed is non-negotiable. Imagine trying to build a house on a tilted foundation—it’s not going to end well.
- Manual vs. Automatic Bed Leveling
If you have a manual printer, use the paper method or feeler gauges. For those with auto-leveling sensors, let your printer do the heavy lifting. - Paper Method vs. Feeler Gauges
Slide a piece of paper under the nozzle and feel for slight resistance. Want more precision? Switch to a feeler gauge for exact measurements.
Calibrating Extruder Steps (E-Steps)
Your extruder controls how much filament is pushed out. Get it wrong, and you’ll either starve or overfeed your print.
- Why Accurate Extrusion Matters
Too much extrusion leaves blobs; too little results in gaps. It’s a delicate balance. - Measuring and Adjusting E-Steps
Use a ruler to measure filament extrusion, compare it to the desired length, and adjust via your printer’s control menu or firmware.
Retraction Settings to Eliminate Stringing
Stringing is like cobwebs—nobody wants them in their prints. Adjusting retraction can help clean things up.
- Testing Retraction Distance and Speed
Start with small adjustments and test on simple prints. - Common Retraction Pitfalls
Avoid excessive retraction, as it can clog the nozzle.
PID Tuning for Temperature Stability
Temperature fluctuations can wreak havoc on prints. PID tuning ensures your printer maintains consistent heat.
- What Is PID Tuning?
PID (Proportional, Integral, Derivative) tuning is like teaching your printer to keep its cool—literally. - Using G-code for PID Calibration
Send a simple G-code command to start the process and save the results to your firmware.
Belt Tension and Axis Alignment
Loose belts can cause layer shifts, while overly tight ones strain the motors. Find the Goldilocks zone—just right.
7. Fine-Tuning Slicer Settings
Adjusting Layer Height and Line Width
Layer height and line width significantly impact the quality, speed, and strength of your prints. Adjusting these settings allows you to tailor prints to your specific needs.
- Layer Height:
- Smaller layer heights (e.g., 0.1mm) improve print detail and surface finish. They’re ideal for intricate models or parts requiring fine resolution.
- Larger layer heights (e.g., 0.3mm) print faster and are suitable for prototypes or functional parts where detail isn’t critical.
- A common starting point is 0.2mm, which balances speed and detail for most nozzles (e.g., 0.4mm diameter).
- Line Width:
- Match the line width to your nozzle diameter for accuracy. For instance, a 0.4mm nozzle works well with a line width of 0.4mm to 0.48mm.
- Increasing the line width slightly improves layer bonding and print strength but may reduce fine detail.
Experiment with these settings on small test prints to find the perfect balance for your specific printer and project.
Optimizing Print Speed Without Sacrificing Quality
Print speed directly affects the time and quality of your prints. While faster prints save time, they can compromise detail and adhesion. Slower speeds often yield better results, especially for intricate designs.
- Standard Print Speeds:
- Factors to Consider:
- Model Complexity: Reduce speed for intricate models to maintain precision.
- Material Properties: Flexible materials like TPU require slower speeds (e.g., 20mm/s) to avoid deformation.
- Printer Stability: High speeds can cause wobbling in less rigid printers, leading to layer shifts or ghosting.
Test different speeds on calibration prints, such as Benchy, to find the best compromise between speed and quality.
How to Tweak Infill Patterns for Strength and Aesthetics
Infill patterns not only determine the internal structure of your prints but also affect their strength, weight, and material usage. Adjusting infill patterns can optimize prints for functionality or aesthetics.
- Common Infill Patterns:
- Grid: A standard pattern that provides decent strength and minimal print time.
- Honeycomb: Offers superior strength and durability, making it ideal for mechanical parts.
- Gyroid: A visually appealing pattern that balances strength and flexibility.
- Choosing the Right Density:
- For lightweight, aesthetic prints, use 10% to 20% infill density.
- For structural parts, increase the density to 50% or higher.
- Layer Height vs. Infill:
Match infill settings with layer height for consistent results. A thicker infill layer paired with fine outer layers can save print time without sacrificing appearance. - Aesthetic Considerations:
Use gyroid or concentric patterns for prints where the infill is visible, such as translucent models.
Fine-tuning slicer settings, including layer height, line width, print speed, and infill patterns, ensures your 3D printer tuning efforts result in optimal performance, stunning aesthetics, and durable parts.
8. Temperature and Material Tuning
The Impact of Temperature on Print Quality
Temperature plays a vital role in 3D printing. Too high, and your prints might look stringy or droopy. Too low, and layer adhesion weakens. Proper tuning of nozzle and bed temperatures ensures consistent results for every print.
How to Tune Your Printer’s Temperature
- Run a Temperature Tower Test:
Download a temperature tower model and print it while gradually adjusting nozzle temperature. Analyze the layers to find the optimal temperature for your filament. - Adjust Bed Temperature:
- PLA: 50–60°C
- ABS: 90–110°C
- PETG: 70–90°C
Material-Specific Tuning Tips
- PLA (Polylactic Acid):
- Print Temp: 190–210°C. However, some high-quality or specialty PLAs may require up to 230°C.
- Bed Temp: 50–60°C
- Fan Speed: High (100%)
- PLA is forgiving, but minor tweaks to retraction or cooling can make a big difference.
- PETG (Polyethylene Terephthalate Glycol):
- Print Temp: 220–250°C. but PETG often performs better at slightly lower speeds to reduce stringing.
- Bed Temp: 70–90°C
- PETG can ooze if the temperature is too high. Slow down retraction speeds for best results.
- ABS (Acrylonitrile Butadiene Styrene):
- Print Temp: 230–250°C. is a good range, note that some ABS types print as low as 220°C.
- Bed Temp: 90–110°C
- ABS is prone to warping, so an enclosure or heated chamber is essential.
Tips for Tuning Cooling
- PLA: Use maximum fan speed to cool layers quickly and prevent sagging.
- ABS and PETG: Reduce fan speed to improve layer adhesion and prevent cracking.
Monitor Your Printer’s Performance
Always monitor the first few layers of a print after adjusting temperatures. This ensures proper adhesion and identifies potential issues early.
9. Testing and Troubleshooting
Printing a Calibration Cube: The First Test
A calibration cube is an essential tool for 3D printer tuning. It’s a small, simple model designed to reveal inconsistencies in your printer’s performance. By examining the cube, you can identify and fix issues such as under-extrusion, layer shifts, and warping.
- How to Print a Calibration Cube:
- Download a standard calibration cube STL file from a reliable source, such as Thingiverse or Printables.
- Use your current slicer settings to prepare the print. Avoid making changes at this stage, as the test is meant to diagnose existing problems.
- Print the cube and carefully observe its dimensions, surface quality, and structural integrity.
- What to Look For:
- Under-Extrusion: Check if there are gaps between lines or weak layer bonding. This indicates the extruder isn’t pushing out enough filament.
- Over-Extrusion: Bulging edges or blobs on the surface suggest too much filament is being extruded.
- Layer Shifts: Misaligned layers often point to loose belts or unstable printer parts.
- Warping: A lifted bottom corner shows poor bed adhesion or incorrect bed temperature.
By understanding the results of the calibration cube, you gain valuable insights into areas that need tuning.
Addressing Issues After Tuning
Even after thorough tuning, some issues might persist. Tuning isn’t a one-and-done process—it’s iterative. Regularly revisiting steps ensures your printer stays in peak condition.
- Layer Shifts:
- Tighten the belts to prevent movement during prints.
- Ensure the printer is on a stable surface to reduce vibrations.
- Stringing:
- Lower the print temperature slightly to minimize filament oozing.
- Increase retraction distance and speed incrementally.
- Uneven Layer Heights:
- Re-level the print bed, ensuring uniform spacing between the nozzle and bed surface.
- Check Z-axis screws for dust or misalignment.
- Inconsistent Extrusion:
- Recalibrate E-steps to match the exact amount of filament extruded.
- Inspect the nozzle for partial clogs and clean it if necessary.
Testing and troubleshooting are ongoing processes in 3D printer tuning, but consistent adjustments yield smoother and more reliable results over time.
Regular Maintenance to Keep Your Printer in Top Shape
Maintenance is the backbone of long-term 3D printer tuning. Neglecting maintenance can lead to recurring issues, reducing the printer’s efficiency and print quality.
- Monthly Maintenance Checklist:
- Clean the Print Bed: Remove filament residue and grease using isopropyl alcohol.
- Inspect the Nozzle: Check for clogs or wear, and replace it if needed.
- Tighten Belts and Screws: Loose components can cause layer shifts or uneven movements.
- Lubricate Moving Parts: Apply a small amount of lubricant to rods and bearings for smooth operation.
- Check Electrical Connections: Ensure all cables are securely connected to prevent intermittent errors.
- Seasonal Maintenance Tips:
- Inspect Firmware: Update the firmware to ensure compatibility with the latest slicer features.
- Recalibrate the Printer: Re-level the bed and recalibrate extrusion steps to account for wear and tear.
- Replace Consumables: Swap out worn PTFE tubes, build plates, or hotend components to maintain print quality.
Proactive maintenance is key to keeping your printer ready for complex prints and reducing the need for constant troubleshooting.
10. Advanced Tuning Techniques
Linear Advance Calibration
Linear advance calibration is a technique that optimizes the flow of filament during acceleration and deceleration. It ensures consistent extrusion, especially around corners and intricate features.
- Why Linear Advance Matters:
Without calibration, filament flow may lag during speed changes, leading to rounded corners or uneven walls. Linear advance compensates for these changes, ensuring smoother and more detailed prints. - How to Calibrate Linear Advance:
- Check Firmware Compatibility: Ensure your firmware supports linear advance (e.g., Marlin 2.0 or newer).
- Print a Test Pattern: Use a calibration model designed for linear advance testing.
- Adjust the K-Factor:
- Start with a low value (e.g., K = 0.05) and gradually increase.
- Observe the model to find the value that eliminates over-extrusion at sharp corners and under-extrusion on curves.
- Applications of Linear Advance:
- Produces cleaner edges and sharper details.
- Reduces stringing in intricate designs.
- Improves layer consistency for mechanical parts.
Exploring Custom Firmware Options
Custom firmware, like Marlin or Klipper, unlocks advanced features for 3D printer tuning. It provides greater control over your printer’s hardware, enabling precise adjustments that standard firmware might lack. Certain printers (e.g., Creality Ender 3) may require a bootloader installation before flashing custom firmware.
- Benefits of Custom Firmware:
- Mesh Bed Leveling: Fine-tune bed leveling across the entire print surface for perfect first layers.
- PID Autotuning: Stabilize hotend and bed temperatures for consistent filament flow.
- Linear Advance Support: Integrate advanced extrusion settings for smoother prints.
- How to Install Custom Firmware:
- Back Up Your Printer Settings: Save your current configurations to avoid losing progress.
- Download the Firmware: Choose the latest release compatible with your printer model.
- Flash the Firmware: Follow the instructions for your printer, often involving an SD card or USB connection.
- Recalibrate: After installation, recalibrate the printer to ensure all settings work with the new firmware.
Custom firmware allows for deeper tuning and is ideal for users looking to push their printer’s capabilities.
Adding Upgrades for Easier Tuning
Upgrades can simplify the tuning process and improve your printer’s performance. Here are a few worth considering:
- BLTouch Sensor:
- Automates bed leveling by measuring multiple points on the print surface.
- Ideal for reducing the hassle of manual adjustments.
- Direct-Drive Extruder:
- Enhances filament control for flexible or abrasive materials.
- Reduces stringing and under-extrusion in complex prints.
- Upgraded Nozzles:
- Hardened steel nozzles withstand abrasive filaments like carbon fiber or wood-filled PLA.
- Nozzle upgrades improve durability and consistency.
- Silent Stepper Drivers:
- Reduces motor noise and vibrations during printing.
- Leads to smoother layer transitions and quieter operation.
Adding these upgrades not only simplifies 3D printer tuning but also elevates print quality and expands the range of printable materials.
11. Printer-Specific Tuning Tips
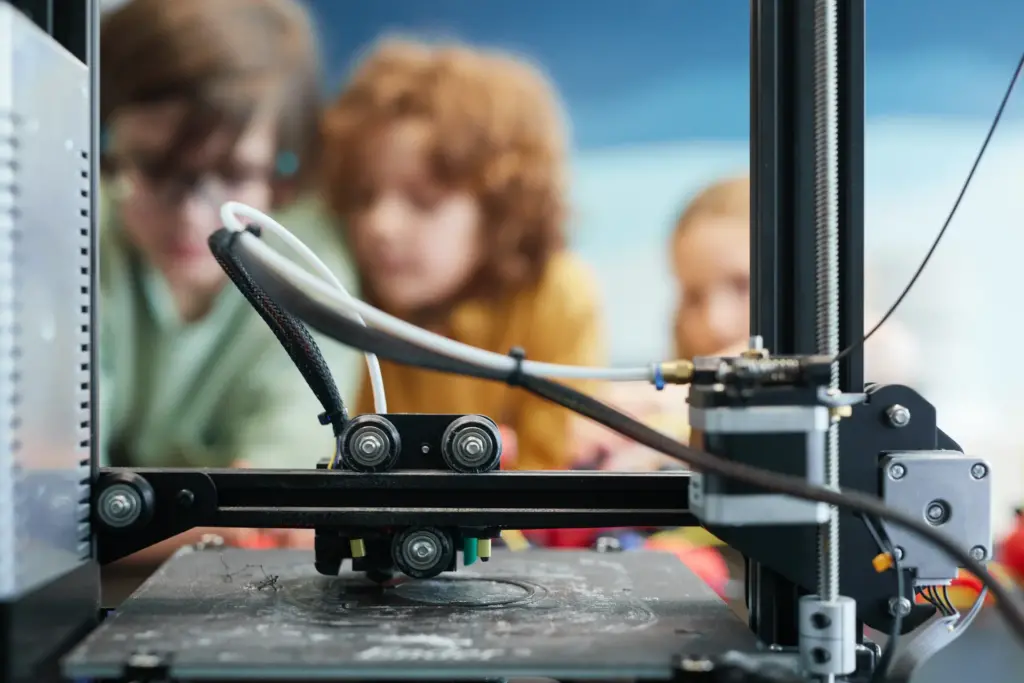
Tailoring Tuning to Popular Printer Models
Every 3D printer model has unique quirks that make tuning slightly different. Whether you’re working with a budget-friendly Ender 3 or a high-end Prusa i3 MK3, knowing the specifics of your printer can save time and effort.
Creality Ender 3 Tuning Tips
- Level the Bed Manually:
Ender 3 models often come without auto-leveling, so mastering the paper method for manual leveling is key. - Upgrade the Springs:
Many Ender 3 users find the stock bed leveling springs inadequate. Upgrading to stronger springs ensures better stability and less frequent leveling. - Calibrate E-Steps:
Factory settings for E-steps on the Ender 3 can be off. Use a calibration print and measure the extruded filament to adjust accordingly.
Prusa i3 MK3 Tuning Tips
- Leverage Auto-Leveling Features:
The Prusa i3 MK3 comes with a PINDA sensor for auto-bed leveling. Make sure the sensor is properly calibrated and updated to the latest firmware for accurate results. - Adjust Live Z Offset:
During your first layer calibration, use the live Z-offset feature to fine-tune the nozzle height dynamically. - Take Advantage of PrusaSlicer:
The PrusaSlicer software is optimized for the i3 MK3. Use its default profiles to get started and tweak settings like retraction and speed for specific filaments.
Anycubic Mega S Tuning Tips
- Bed Adhesion Tricks:
The Ultrabase print bed on the Anycubic Mega S provides excellent adhesion, but regular cleaning with isopropyl alcohol ensures consistent performance. - Fine-Tune Retraction Settings:
This model benefits from lower retraction speeds to prevent stringing, especially with PLA and PETG. - Upgrade the Firmware:
Updating to custom firmware like Marlin can unlock advanced tuning options for smoother prints.
12. In-Depth Slicer Customization
Why Slicer Settings Are Critical
A slicer converts your 3D model into instructions your printer understands, making it a crucial part of the tuning process. Proper slicer customization can dramatically improve print quality, reduce failures, and save time.
Basic Slicer Settings to Adjust
- Layer Height:
- Smaller layer heights (e.g., 0.1mm) provide finer detail but take longer, while larger layers (e.g., 0.3mm) print faster with less precision. The maximum layer height rule: it should not exceed 75% of the nozzle diameter for consistent extrusion. For a 0.4mm nozzle, this means a max layer height of 0.3mm.
- Line Width:
- Match the line width to your nozzle diameter for better accuracy. For a 0.4mm nozzle, a line width of 0.4mm–0.48mm works well.
Advanced Settings for Improved Results
- Retraction Settings:
- Distance: Adjust how far the filament is pulled back to reduce stringing.
- Speed: Find the sweet spot between too slow (causing blobs) and too fast (risking clogs).
- Infill Density and Pattern:
- Low-density infill (10–20%) saves filament, while high-density infill (50–100%) improves strength.
- Patterns like honeycomb or gyroid balance aesthetics and durability.
- Print Speed:
- Slower speeds (e.g., 40mm/s) improve detail, especially for complex parts.
- Higher speeds (e.g., 80mm/s) are better for rapid prototyping.
Optimizing for Specific Materials
- PLA: Lower temperatures (190–210°C) and fan speeds at 100% help prevent stringing.
- PETG: Higher temperatures (220–250°C) and slower print speeds reduce oozing.
- ABS: Enclosed environments and moderate cooling prevent warping.
Using Slicer Profiles for Efficiency
- Many slicers, like Cura or PrusaSlicer, offer pre-made profiles for popular printers and materials. Start with these and tweak as needed for your setup.
Plugins and Advanced Tools
- Cura: Try plugins like “Mesh Tools” or “Calibration Shapes” for added functionality.
- OctoPrint Integration: Use plugins to directly adjust slicer settings on the fly.
13. Conclusion
Mastering 3D printer tuning is the secret to turning failed prints into flawless creations. From bed leveling to slicer settings, every step brings you closer to perfection. Remember, tuning isn’t just a task—it’s an art. So grab your tools, experiment boldly, and watch your printer come alive like never before.
14. FAQs About 3D Printer Tuning
- What’s the first thing to check when tuning a 3D printer?
Always start with bed leveling—it’s the foundation of every print. - How often should I tune my printer?
Tune whenever you notice print issues or after major upgrades. - What’s the easiest way to calibrate E-steps?
Measure filament extrusion and adjust settings in your firmware. - Do slicer settings affect tuning?
Absolutely! Fine-tuning slicer settings can drastically improve print quality. - Can I automate the tuning process?
Yes, with upgrades like auto-leveling sensors and advanced firmware.
Resources
- https://www.prusa3d.com/page/prusaslicer_424/
- https://ultimaker.com/software/ultimaker-cura/
- https://teachingtechyt.github.io/calibration.html
- https://octoprint.org/
- https://www.klipper3d.org/
- https://marlinfw.org/
- https://www.3dbenchy.com/
- https://www.printables.com/
- https://www.thingiverse.com/